United International Journal for Research & Technology
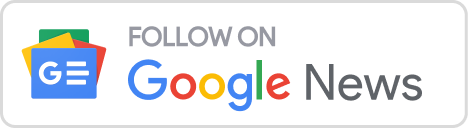
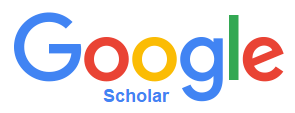
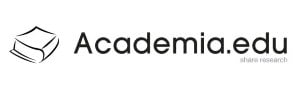
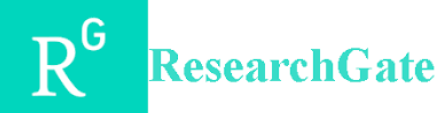
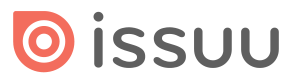
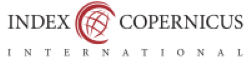
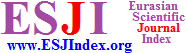
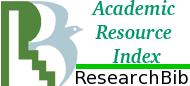
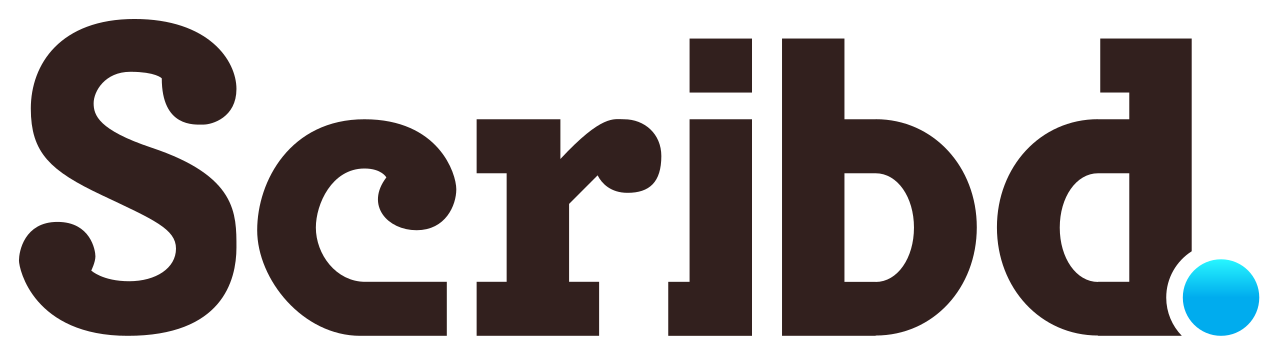
Why UIJRT?
Peer Review Journal
Peer review is the evaluation of work by one or more people with similar competencies as the producers of the work. It functions as a form of self-regulation by qualified members of a profession within the relevant field.
Research & Review Topics
You can publish your paper on different topics and subjects like Artificial Intelligence, Computer Science, Mechanical Engineering, Electrical Engineering, Civil Engineering & etc. It is totally depend on your area of publication.
Fast Indexing Journal
Our journal's papers are indexing on multiple website like Google Scholar, Research Gate, Academia, Sribd, Issuu, ResearchBib, SlideShare, etc. UIJRT is a fast indexing journal on the internet.
Free Certificate
Author(s) can collect their free E-certificate in PDF format after the publication of paper on UIJRT. We are not charging any fee for certificate. It is free for all author globally.
Open Access Journal
Open access (OA) refers to free, unrestricted online access to research outputs such as journal articles and books. OA content is open to all, with no access fees. One involves publishing articles or books via the OA route on a publisher's platform (often referred to as gold open access).
ISSN Approved Journal
UIJRT is an ISSN approved journal. ISSN: 2582-6832 is the ISSN number of United International Journal for Research & Technology (UIJRT). An International Standard Serial Number is an 8-digit serial number used to uniquely identify a serial publication, such as a magazine.